Polygon Turning
Polygon Turning
Trojan Special Fasteners Ltd has the capability to produce square and hexagon polygon nuts from round bar or nuts.
Polygon turning is a machining process in which a polygonal shape is cut into the outer diameter of a cylindrical workpiece. The process uses a specially shaped cutting tool, often a single-point tool, to create the polygonal shape. The cutting tool is typically mounted on a lathe and is moved along the axis of the workpiece while it rotates. This process is also known as "polygon machining" or "polygon turning". Some common shapes that can be produced through polygon turning include squares, hexagons, octagons, and decagons. It is used in various industries such as aerospace, automotive, and medical device manufacturing.
Machine setup and operating time is generally very fast as no indexing is required between jobs.
The process of polygon turning rapidly produces a part with flats by synchronising rotation of the spindle and the tool. It is an alternative to milling each surface individually and it does this with speed and relative accuracy.
The typical tool holder has four different positions for insert cartridges. For even-numbered (2, 4, 6 and 8) sided parts, the cutter head typically rotates at a 2:1 ratio with the main spindle.
How you populate the tool holder determines the number of flats:
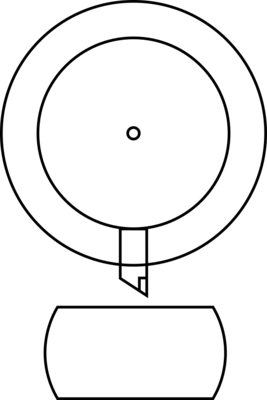
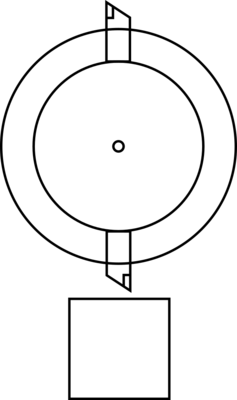
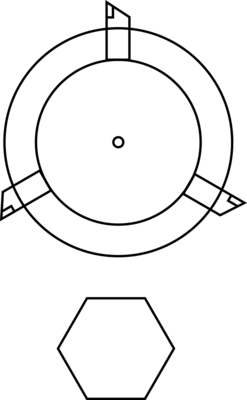
This method can also be used to produce collar nuts and flange nuts.
It is being increasingly used where hexagon or square bar is no longer available so we must turn polygon from round.
Reducing Polygon
We have the ability to mount internally threaded parts and reduce their polygon size. This is common where parts are made for restoration services and could have been machined from any available hexagon at the time and then reduced to the actual across flat that is needed. This is a relatively simple and quick process although it should be noted that due to the manual indexing of this process, more than 1mm reduction is necessary in order to maintain polygon accuracy.